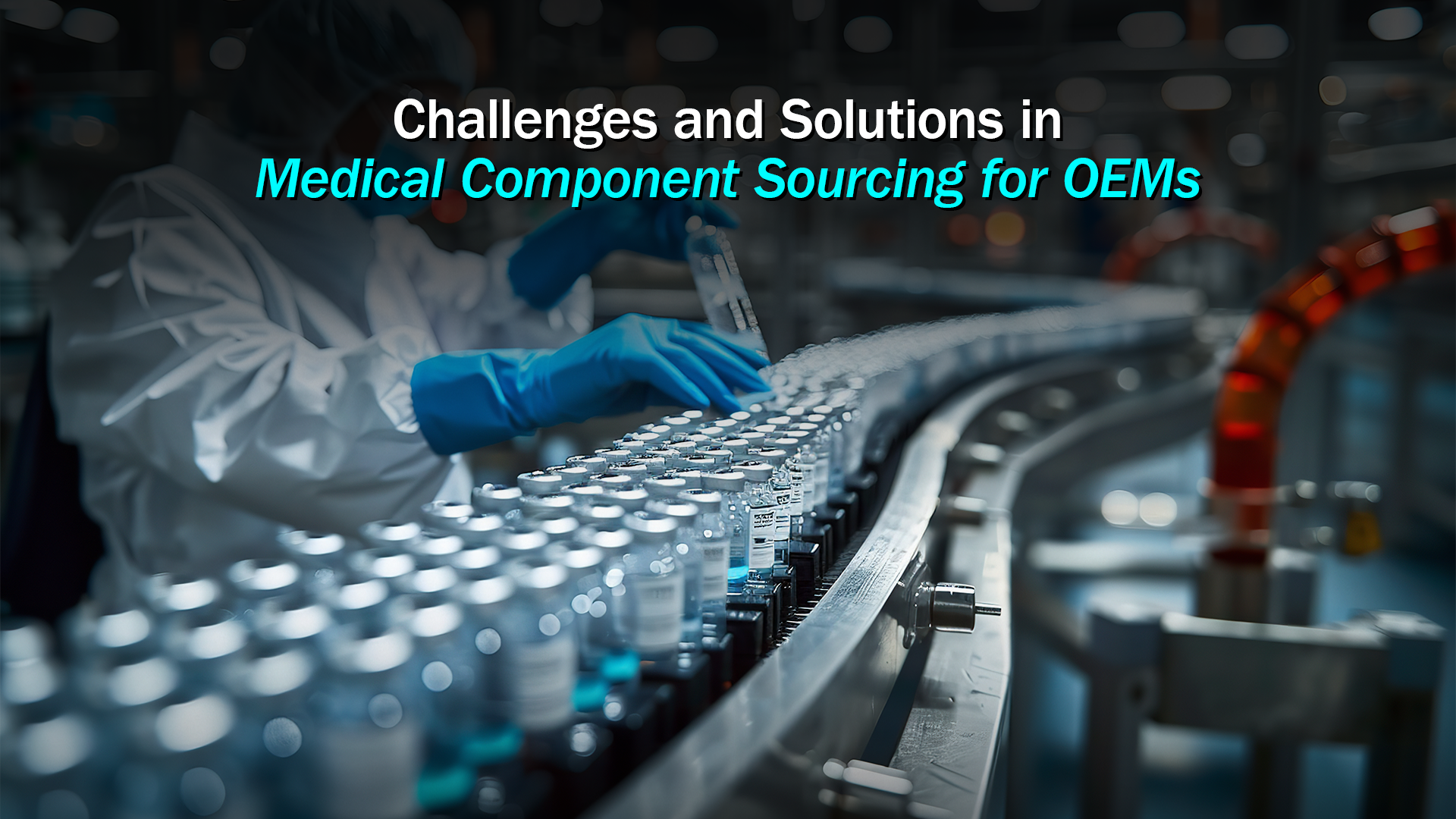
Sourcing precision-machined components is a critical process for OEMs looking to meet production demands with high-quality, cost-effective solutions. As manufacturing grows more complex and globalized, sourcing machined parts requires a deep understanding of technical specifications, supplier capabilities, and industry trends.
This article explores the fundamentals of machining component manufacturing, including defining machining requirements, selecting the right suppliers, mitigating risks, and adapting to emerging market trends to ensure a resilient and efficient supply chain.
Industrial machining refers to the process of shaping raw materials, like metal and plastic, into custom parts and components. These components are used across industries, including automotive, aerospace, electronics, and medical devices. Machining techniques vary based on the requirements of the end product, and common processes include milling, turning, drilling, and grinding. With the emergence of high-precision technologies like Computer Numerical Control (CNC) machining, the field has advanced significantly, offering higher levels of precision and consistency.
There are multiple machining techniques, each serving specific functions:
● CNC Machining: Utilizes computerized controls to remove material precisely from a workpiece.
● Milling: Involves rotating cutting tools that shape and hollow out materials.
● Turning: A lathe-based method that rotates the workpiece to achieve the desired shape.
● Grinding: Used for polishing and finishing surfaces to achieve smoothness and specific dimensional tolerances.
Each method has its advantages and limitations, making the choice of process critical when briefing Industrial Product Sourcing Company.
Before sourcing, Industrial Product Sourcing Partners need to define their specific requirements. Key factors include:
● Material Type: The choice of material impacts both the machining process and the cost. Common materials include steel, aluminum, titanium, and plastics, each requiring specific tools and techniques.
● Precision and Tolerance: These specifications determine the accuracy needed in dimensions. Industries like aerospace and medical devices often require ultra-high precision, while other industries may accept broader tolerances.
● Volume: Whether high or low, production volume affects sourcing options. High-volume needs might call for scalable providers, while low-volume or custom needs may require specialized providers.
● Budget Constraints: Cost implications of machining vary widely based on material, complexity, and precision requirements. Transparent budgeting helps identify potential providers who can deliver within financial limits.
The process of sourcing involves identifying suitable suppliers who meet quality, cost, and delivery expectations. This includes domestic suppliers and, increasingly, overseas vendors due to globalization and competitive pricing. Here are key considerations:
● Domestic Sourcing: Local suppliers generally offer faster turnaround times, easier communication, and reduced shipping costs. They may also have better regulatory compliance, reducing quality and liability risks.
● Overseas Sourcing: Overseas suppliers, especially from regions like Asia, often provide competitive pricing. However, challenges include longer lead times, potential communication barriers, and variable quality standards. To manage risks, many businesses now rely on third-party quality inspections via Industrial Product Sourcing Partners for overseas orders.
● Technical Expertise: A supplier’s proficiency in specific machining processes, such as CNC machining or complex assemblies, is essential.
● Quality Certifications: Certifications like ISO 9001 (Quality Management) or AS9100 (Aerospace Quality Management) indicate a supplier’s commitment to quality standards.
● Capacity and Scalability: Suppliers should have adequate machinery, skilled labor, and resources to handle both current and future volume needs.
● Lead Time and Delivery Reliability: Reliable delivery times ensure that production schedules are not delayed, and a good supplier should provide transparency in lead-time estimates.
Risk management is integral to sourcing in any industry, but particularly in machining, where quality and delivery are paramount. Here are some strategies:
● On-Site Audits and Inspections: Physical audits can be performed to verify supplier capabilities, equipment conditions, and adherence to quality processes.
● Sample Testing: Requesting samples or small batch orders allows buyers to evaluate the quality before committing to larger orders.
● Third-Party Verification: External inspections can add an extra layer of quality control, especially when sourcing overseas. To make it seamless, opt for an Industrial Product Sourcing Company.
● Non-Disclosure Agreements (NDAs): Protecting intellectual property is vital, especially for unique designs and proprietary processes.
● Penalty Clauses: Including penalties for delays or non-compliance with specifications can incentivize suppliers to uphold standards.
● Long-Term Contracts: For reliable suppliers, long-term contracts can stabilize pricing, reduce sourcing times, and build trust.
The landscape of industrial machining is rapidly evolving, with new technologies and practices transforming sourcing practices. Here are some key trends:
● Additive Manufacturing: 3D printing is now a viable option for prototypes and small-batch production, providing design flexibility and reducing material waste.
● Smart Machining and Industry: Automation and IoT integration allow for real-time monitoring of machining processes, increasing efficiency, and predictive maintenance to minimize downtimes.
Many manufacturers are now seeking environmentally friendly machining practices. This includes using recycled materials, optimizing waste reduction, and adhering to sustainable practices that minimize the carbon footprint.
Online marketplaces and platforms are gaining popularity in being your Industrial Machining Sourcing Partner. These platforms connect buyers with a range of suppliers globally, providing transparency, competitive pricing, and streamlined communication. They also often feature review systems and performance metrics, which simplify the process of evaluating potential suppliers.
Industrial machining sourcing is a complex but crucial component of modern manufacturing. It requires a blend of technical understanding, strategic planning, and an Industrial Machining Sourcing Partner. By carefully assessing machining requirements, evaluating supplier options, and employing risk mitigation strategies, businesses can secure high-quality machining services that meet both budgetary and production needs. Embracing emerging trends, such as digital sourcing platforms and sustainable practices, can further enhance the sourcing process. As industries continue to evolve, effective machining sourcing will remain a vital element in ensuring operational efficiency, product quality, and market competitiveness.